- Home
- Support
- Case Studies
- 1001
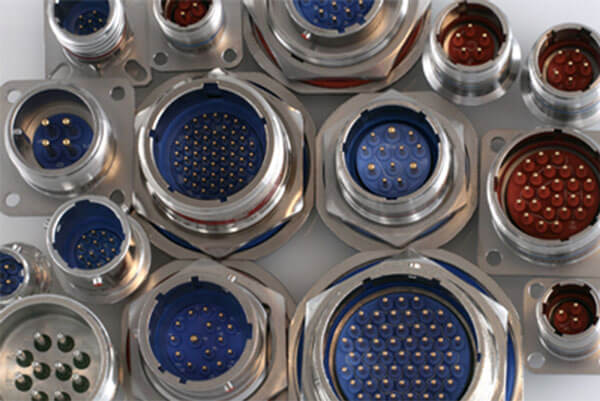
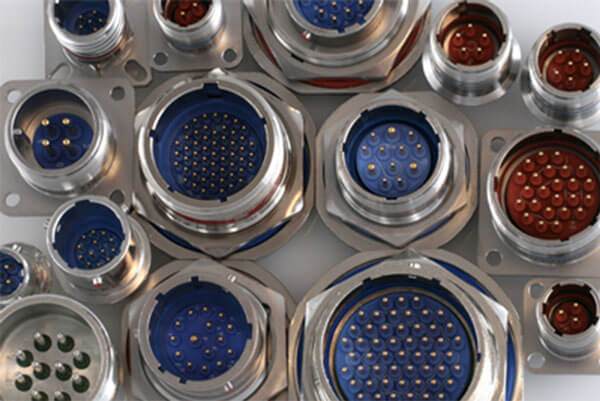
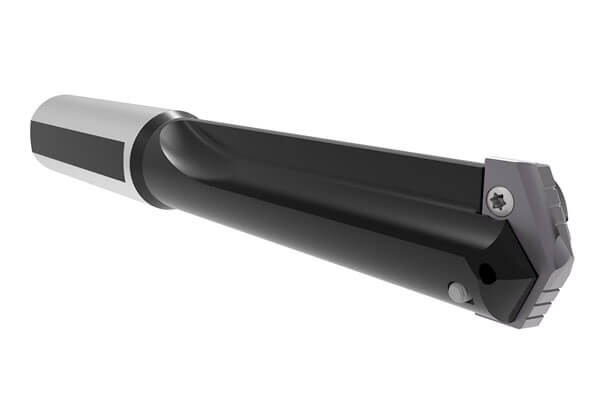
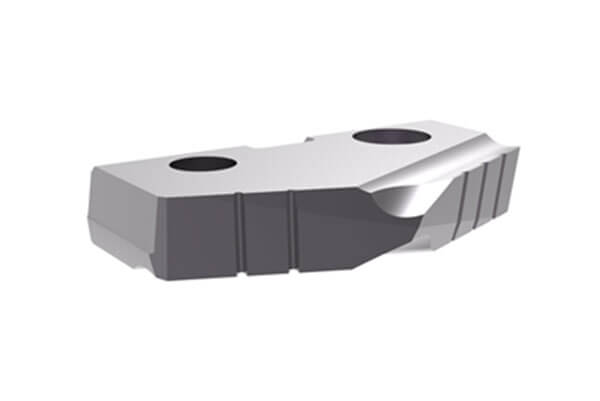
Code
1001
The Challenge
The customer manufactures components for the aerospace industry using a Mori Seiki lathe with a bar feeder running with 300 PSI (20.684 bar) oil coolant. They are machining aerospace connectors made from 6061-T6 aluminum.
Unsatisfied with this procedure, the customer needed to increase tool life and complete the entire drilling process in one operation.
The Original T-A completed the process in one operation and provided significant cost-saving advantages for the customer.
Product: | Original T-A |
Objective: | Increase tool life |
Industry: | Aerospace |
Part: | Connector |
Material: | 6061-T6 aluminum |
Hole Ø: | 1.4375" (36.513mm) |
Hole Depth: | 6.0" (152.4mm) |
The Solution
The Original T-A Drill
- Holder: 23030S-150L
- Insert: 1C23A-0114
Measure | Competitor | Original T-A |
---|---|---|
RPM | 3000 | 3000 |
Speed | 1129 SFM (344.119 M/min) | 1129 SFM (344.119 M/min) |
Feed Rate | 0.012 IPR (0.305 mm/rev) | 0.022 IPR (0.559 mm/rev) |
Penetration Rate | 36 IPM (914.4 mm/min) | 66 IPM (1676.4 mm/min) |
Cycle Time | 45 sec | 10.5 sec |
Tool Life | 1250 holes | 10500 holes |
The Advantages
The Original T-A provided:
- 23% cycle time decrease
- Lowered the cost of production
- Increased tool life