- Home
- Support
- Case Studies
- 1003
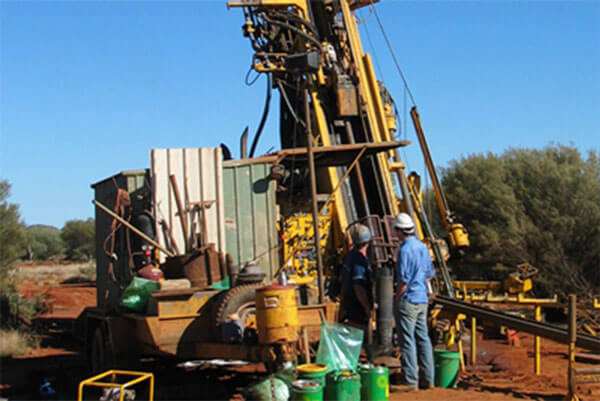
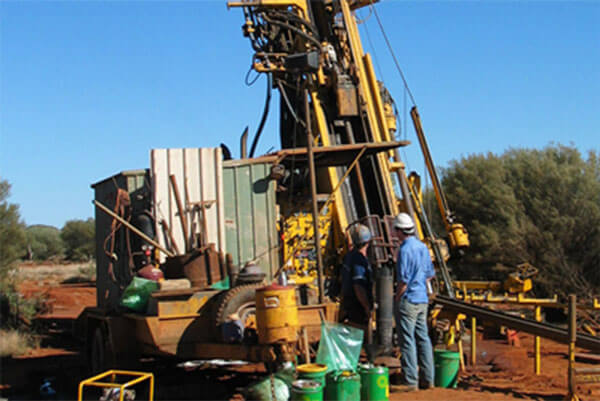
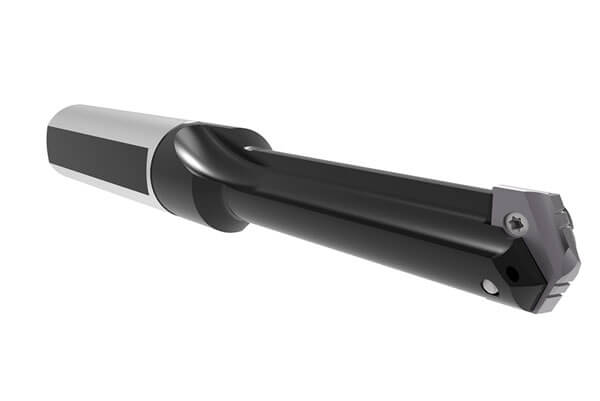

Code
1003
The Challenge
A contract machine shop repairs and maintains equipment for the oilfield industry. They are machining a down hole mud injection tube used in offshore drilling. The tube is made from heat treated alloy steel. They are using a manual lathe running with water soluble oil coolant through the tool with a rotary coolant adapter.
Seeking to improve the production process, the customer needed to reduce the cycle time and decrease the cost of production.
The Original T-A lowered cycle time and increased tool life.
Product: | Original T-A |
Objective: | Decrease cycle time |
Industry: | Oil & gas/petrochemical |
Part: | Mud injector tube |
Material: | Heat treated alloy steel |
Hole Ø: | 0.75" (19.05mm) |
Hole Depth: | 10" (254mm) |
The Solution
The Original T-A Drill:
- Holder: 27010S-100L
- Insert: 151A-0024
Measure | Competitor Drill | Original T-A |
---|---|---|
RPM | 475 | 750 |
Feed Rate | 0.005 IPR (0.127 mm/rev) | 0.0065 IPR (0.165 mm/rev) |
Cycle Time | 4 min 42 sec | 2 min 33 sec |
Tool Life | 8 holes | 11 holes |
The T-A offered 59.12% cost per hole savings over the competitor tooling. |
The Advantages
The Original T-A provided:
- 45% cycle time decrease
- Lowered the cost of production
- Increased tool life